In recent years, the real estate and construction industries have been deeply affected by the pandemic, supply chain issues, and a new federal infrastructure bill that promises a considerable amount of money to build new projects and rehabilitate the old. New York City has been at the forefront of many of these changes.
Yet still, the city is seeing a thriving investment and growth in its life sciences industry, a sector that recently received $1 billion in funding from U.S. administration. With these new investment plans in place, New York City, and the life sciences sector in particular, deserves a construction model better suited to handle this fast expansion.
At Talisen Construction, we are guided by a unique focus on collaboration with our project team partners and a goal of innovating within our space to identify crucial elements of the construction process that can be improved. With the expansion of the life sciences sector in NYC, we are of the opinion that the design-build method is the project delivery method that best allows collaboration and innovation to thrive; driving these projects to achieve their greatest outcomes and speed to market.
But, what exactly is design-build? This is a question many in the region may ask as it is uncommonly used in the private sector. The design-build approach uses a single entity to provide both design and construction services for the client. For property owners and developers who are interested in getting their projects completed efficiently, the design-build model makes sense.
Design-Build Background and Approach
Today, the collective perception of the design-build approach has fortunately shifted, with the majority of contractors, customers, government officials, and jurisdictions recognizing its immense value. Richard Thomas, director of state and local legislative affairs of the Design-Build Institute of America, predicts a “design-build Renaissance” across the NYC area over the next decade.
In this time of change it’s important to pay attention to a commercial construction model that’s used throughout the country with the hopes that it will become more widely adopted here in New York City.
On December 31st, 2020 the New York City Public Works Investment Act was signed into law. This bill authorized NYC agencies to utilize design-build for City projects. The DOT and Dept. of Design and Construction may now award design-build contracts under specific conditions for projects costing $10 million or more.
The Dept. of Parks and Recreation and other projects costing at least $1.2 million – including cultural institutions, security improvements, and improved sidewalk access for those with disabilities – may also utilize the design-build approach. Additionally, the Dept. of Environmental Protection, the Health and Hospitals Corp., the Housing Authority, and the School Construction Authority have also received permission to use the design-build method of delivery.
However, private industries and their building partners such as architects, engineers, and contractors should also begin to recognize design-build as a way to construct in a more efficient manner throughout New York City.
Design-Build Advantages
At Talisen Construction, we have engaged our project partners in these methods over the course of some vital projects, and have pinpointed the below areas as key differentiators in the design build method:
A Single Point of Responsibility Makes Sense
Commercial construction projects are complex. Throughout the process, there will be questions that need answers, problems that need solutions, and decisions that need to be made. The design-build model’s greatest strength is that it consolidates all project oversight responsibilities into a single entity. This saves time, reduces confusion and miscommunication, and increases accountability.
Design-build Makes Meeting Tight Deadlines Realistic
Not every New York City commercial construction project needs to happen on an accelerated timeline, but many do. Additionally, many builds must be completed without disrupting the other occupants in the building or their businesses. Because the design-build model uses a single entity to provide all necessary design and construction services, collaboration and communication processes are significantly streamlined. According to the Design-Build Institute of America, an industry trade group, design-build projects are 30% faster to market than projects built using multiple firms.
Significant Cost Savings Boost Project Profitability
We’ve known for some time that the design-build model saves money. As reported by Crain’s New York in 2011, the city researched the issue and found design-build projects to be 27% less costly; in the interim, the development of other construction technologies and lean project management mean that greater savings can be realized.
Innovation & Quality of Construction
Throughout Europe and the parts of the US where the design-build model is the norm for commercial construction projects, a higher degree of innovative design and quality construction has become the norm.
Design-Build Methods in Action
While there have been few project examples in the private sector of the design-build contract in action, Talisen has engaged in multiple projects wherein the design-build method was utilized despite not in contract (i.e. early collaboration with the end-user during pre-construction with key inputs by architects and engineers throughout the process). Without this method it is unlikely that these projects would have achieved the speed-to-market and budget efficiency that they did:
Northwell Health – Lynbrook MOB
In 2016, Northwell Health collaborated with Talisen to assist in transforming a 27K sq. ft former water treatment plant into a premier medical office building offering full cardiology, family medicine, gastroenterology, internal medicine, and pulmonology services. This 1940’s structure was in a very desirable location, but a significant amount of work needed to happen in a very short time frame. Opening a new facility in Lynbrook was a top priority for Northwell Health, and market demands dictated that construction needed to happen quickly.
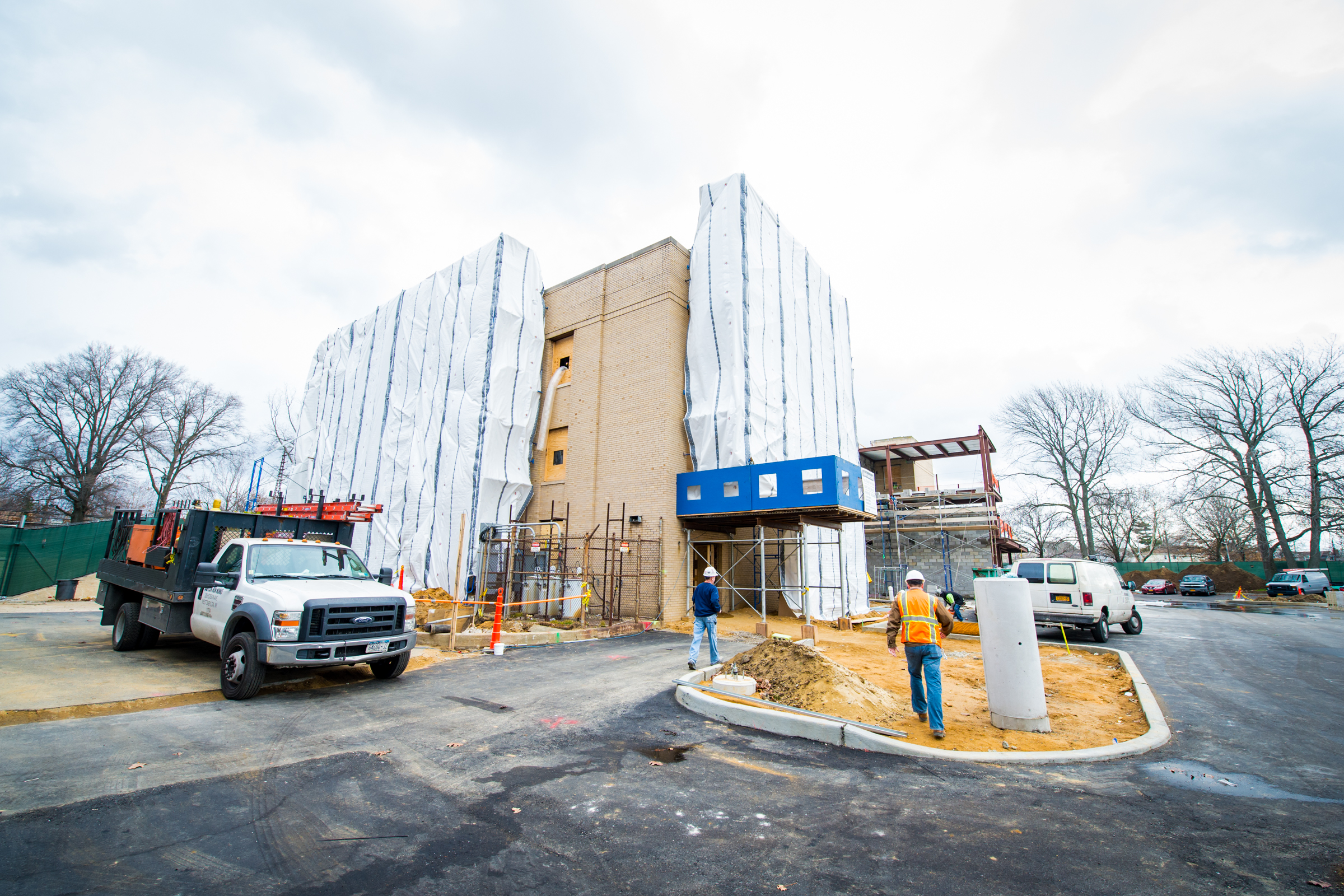
An up-close view of the facade restoration at Northwell’s Lynbrook Medical Office Building
Without an engineer, architect, or any preliminary drawings Talisen was tasked with assembling a team that could expedite the design and building process to achieve the project deadline. In line with our company precept of pursuing perfection in all that we do, Talisen’s team set forth to renovate the dated structure through well-planned and coordinated collaboration with our project partners, client, and subcontractor teams.
The initial set of plans allowed for 400 sq. ft of brick repair, based on a visual assessment from grade. As part of the pre-construction phase, Talisen brought in a masonry contractor for a closer look. When viewed from scaffolding, it became clear that more than 80% of the façade would need to be replaced due to weather damage and structural insufficiency. The scope of work for this portion of the project had increased 350%.
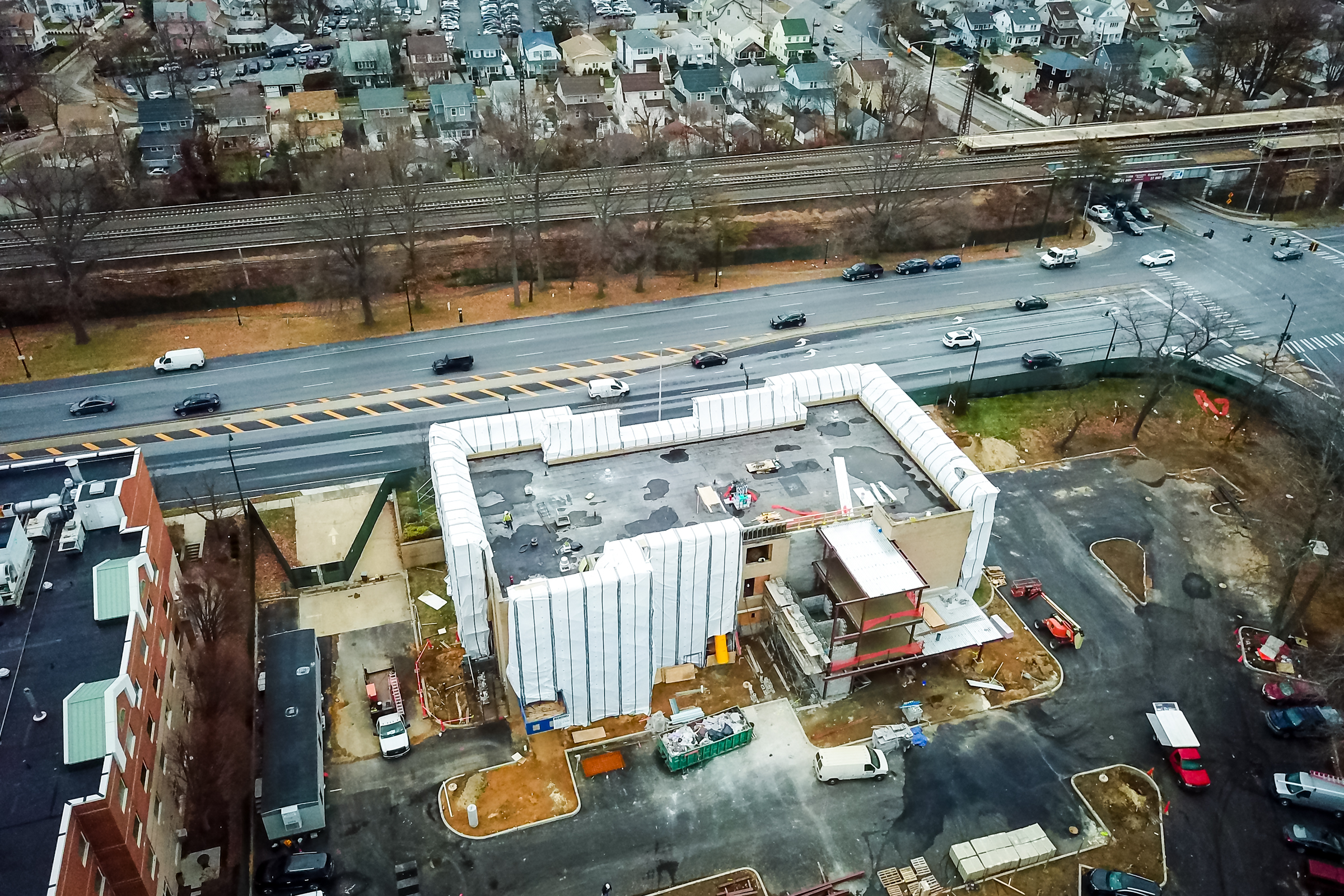
An aerial view of the facade work at Northwell’s Lynbrook Medical Office Building
The pre-construction and design-build process proves its worth in moments like these. With Northwell’s approval, discretionary funding was used to do a detailed engineered assessment. This assessment was brought to the masonry contractor, to develop a detailed drawing set and was then submitted to the architect and Northwell. The decision was made to have the work performed on an expedited basis, ensuring project deadlines would be met.
The rapid action saved about 35 days of additional work identified – before the project started.
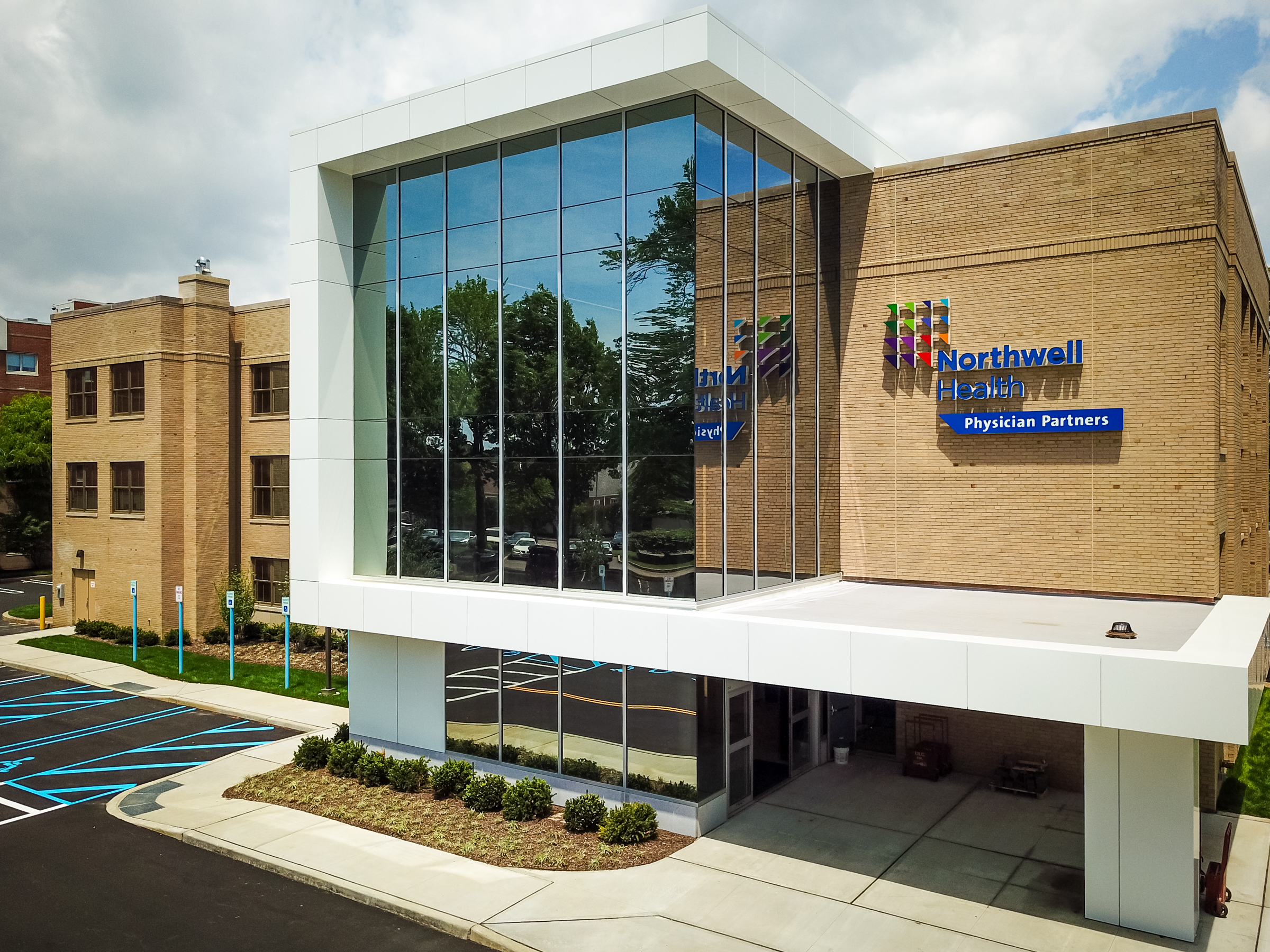
Northwell Health’s Medical Office Building in Lynbrook, NY
Initially slated for a full, 13-month construction period at the point of schematic design, the Northwell Health Lynbrook Medical Office Building was completed on an expedited timeline of just 8 months.
The project completed within 1% of the GMP budget – less than $250 – with savings attributable to speed to market amounted to more than $817,000. Most importantly, the project was done safely through the strong efforts of the dedicated project team who sought to turn Northwell’s vision into reality.
Next Steps for NYC
Distilling the elaborate design and construction method to one point of contact, as in the design-build model, allows the client to streamline the entire process and achieve greater speed to market. In an environment like New York City where new life sciences laboratories are being encouraged by the local governing bodies, the design-build model offers a faster and more efficient way to bring these products to fruition. The cities landscape of older buildings in need of repair or adaptable for life sciences (large slab-heights, available mechanical space, etc.) allows key stakeholders to capitalize on filling this need in our city. The design-build model of construction fits into that puzzle beautifully to address the sometimes-complicated design issues and challenges facing these builds.
If you’re interested in discussing more about design-build in New York City, or life sciences projects in general, please contact us.
Comments 1
looks great!1